Industrial decarbonisation
The decarbonisation of industry through renewable energies
R&D Energy efficiency Decarbonisation
Decarbonisation of industry through electrification is essential to tackle climate change, use energy more efficiently and foster innovation. This is a crucial step towards a more sustainable and resilient future, so let's look at the best options to achieve this by assessing the various alternatives.
A large part of industry's energy needs comes from so-called industrial heat, which is used in industrial processes. Heat is needed for a wide range of industrial applications, such as heating fluids, generating steam, carrying out chemical reactions, drying materials, melting metals or heating facilities. Moreover, because of its wide variation in applications, industrial heat often requires different temperature levels and quantities of heat, depending on the specific needs of each process.
Historically, fossil fuels such as natural gas, oil and coal have been used to generate this heat in boilers and industrial furnaces. However, the growing focus on sustainability and the quest to reduce greenhouse gas emissions means that industry is increasingly looking to renewable and more energy-efficient sources of heat. There is no doubt that the decarbonisation of industry through electrification is fundamental to progress in the fight against climate change. In addition, electrification allows for more efficient energy use while enabling the implementation of more advanced control and monitoring technologies, resulting in more accurate and efficient management of industrial processes.
If you are interested in learning more about the fight against climate change, discover what the energy transition is and how Iberdrola is committed to a cleaner, more responsible and smarter model.
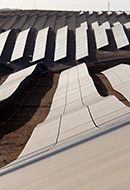
Decarbonisation
Regulatory principles and actions to fight climate change.
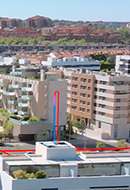
Heat networks
Innovation in Thermal Management for a Sustainable Future.
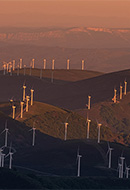
Electrification
Find out how it contributes to each sector and why it is key to tackling climate change.
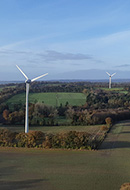
ETaaS
Your partner on the road to industrial electrification.
Renewable industrial heat alternatives to decarbonise industry
Given the need for different levels of heat, there are a variety of renewable alternatives to provide green industrial heat that will enable progress in the decarbonisation of industry. So, depending on the temperature sought, the best options will vary.
High temperatures, of more than 500º C
In the case of high temperatures, electric furnaces are available for many applications. In other cases, when this is not possible, biomethane or green hydrogen are the best options. Biomethane is a form of methane, the main component of natural gas, but its production comes from renewable rather than fossil sources. Therefore, where there are adequate resources and an established natural gas infrastructure, biomethane can be an attractive and sustainable option for industrial heat, although the availability of biomethane is limited.
Green hydrogen, which is produced from renewable energy sources, can be used as a fuel in boilers and industrial furnaces, replacing traditional fossil fuels. Green hydrogen has a high energy density and can be stored and transported, allowing for greater flexibility in heat distribution and utilisation. However, it is important to note that large-scale production of green hydrogen requires greater availability of renewable energy and adequate infrastructure for its production and distribution.
High temperatures of more than 500º C
- Biomethane
- Green hydrogen
- Renewable installation
- For medium and high temperatures, between 100°C and 500°C
This is the largest range of renewable industrial heat options to support the decarbonisation and electrification of industry. One of these is biomass, through different forms such as wood chips, agricultural and forestry waste from nearby forests, waste from the food industry or biogas, which mainly contains methane and, like the above, can also be used as a fuel in boilers to generate industrial heat. Its main advantages include the fact that it uses renewable waste that would otherwise be discarded, which contributes to waste and emissions reduction, and that it is a local energy source, which can reduce dependence on imported fossil fuels.
Another solution is electric boilers which, instead of burning fossil fuels such as natural gas or oil, use electrical resistors to convert electrical energy obtained from renewable sources into heat. Their main features include high energy efficiency compared to combustion boilers, no direct emissions of pollutant gases or carbon dioxide during operation and precise temperature control, which can be beneficial in processes where strict temperature control is required.
In cases where medium and high temperatures are required, thermal storage can also be considered. This technology makes it possible to store energy generated from renewable sources and to use this generated heat in industrial processes at times when it is not immediately required. There are different thermal storage methods used in industrial heat:
- Sensible heat storage: A medium or material is used that can retain and release heat as a function of temperature changes. Most commonly used are stones, bricks, molten salts or other phase change materials.
- Latent heat storage: Heat is stored in a material that changes phase during the thermal charging and discharging process and when it changes state, e.g., from solid to liquid or liquid to gas, it absorbs or releases a large amount of latent heat. Examples include salts, paraffins or organic phase change materials.
- Chemical heat storage: Here storage occurs through a chemical reaction that absorbs or releases thermal energy. Chemical materials that can decompose or react chemically are used to store or release heat. Examples include the use of metal hydrides or endothermic and exothermic reactions.
The main advantages of thermal storage are that thermal energy can be managed efficiently, as heat can be stored during periods of low demand and used at times of high demand, thus optimising the use of intermittent renewable energy sources, such as solar or wind power. In addition, it can improve the flexibility and stability of the electricity system, as it functions as a thermal battery, harnessing surplus renewables and eliminating spillage, facilitating greater penetration of renewables in the system.
For medium and high temperatures, between 100º and 500º C
- Biomass
- Thermal storage
- Electric boilers
- Renewable installation
- For low temperatures, less than 100°C
If renewable options are sought for industrial heat at low temperatures and to enable progress towards the decarbonisation of industry, aerothermal and heat pumps are the most suitable. Aerothermal energy uses ambient air as an energy source to generate heat through the use of heat pumps. These heat pumps extract heat from the air, even at low temperatures, and transfer it to a heating or hot water system for use in industrial applications. This makes them more energy efficient compared to conventional heating technologies. For each unit of electrical energy consumed, a heat pump can generate several units of thermal energy.
In addition, aerothermal and heat pumps do not generate direct greenhouse gas emissions during operation and are very versatile, they can be used for industrial heating applications, for specific processes in industry or for air conditioning systems in combination with refrigeration units, which provides greater flexibility in temperature regulation in different processes. They also do not require a specific area for storing fuels or installing combustion equipment.
Low temperatures, less than 100ºC
- Aerothermy
- Heat pumps
SEE INFOGRAPHIC: Renewable industrial heat alternatives to decarbonise industry [PDF]
Heat networks: what are they?
Heat networks that reuse surplus heat from a production process for a second use are known as waste heat recovery networks or process heat networks. These networks harness the excess heat generated in industrial activities and channel it to additional uses, for example, to cover heating needs in nearby buildings. In this way, energy efficiency is maximised by preventing heat from being wasted and dissipated into the environment, thereby reducing additional energy demand and, consequently, carbon emissions. However, for this type of network to be effective, it requires that either the industrial processes or the buildings in which it is to be used are in close proximity. In this way, waste heat can be efficiently transferred through a network of pipes to the points of use.
It is therefore an effective way of harnessing waste energy from industrial processes and reducing their environmental impact. These grids improve energy efficiency, offer economic benefits and contribute to the transition towards a more sustainable model.