Floating offshore wind
Floating offshore wind power: a milestone to boost renewables through innovation
Wind power is stronger in the ocean than on land, hence the development of offshore wind in recent years. Until recently, because they were based on fixed structures, they could not be installed in very deep or complex seabed locations, something that has changed with the advent of floating structures. Wind turbines can now be installed on these platforms, which are anchored to the seabed by means of flexible anchors, chains or steel cables.
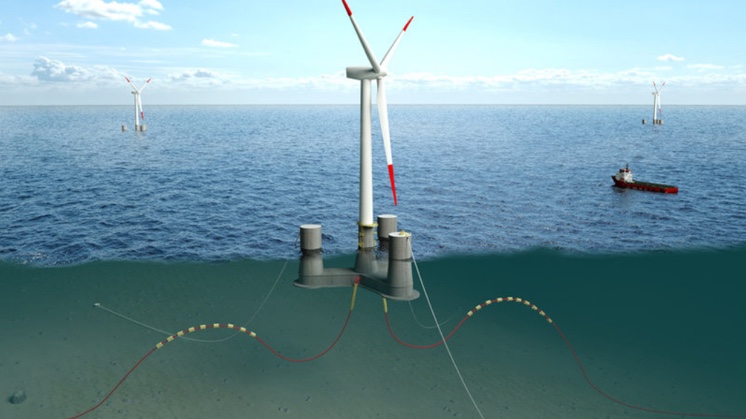
The main challenge facing humanity today is to achieve a green and sustainable planet. To achieve this, renewable energies will play a fundamental role and the effort to innovate in the sector is particularly intense. Advances invite optimism and, in this article, we will focus on one of them: floating offshore wind energy, one of the most promising derivatives.
What is floating offshore wind energy
First of all, let us define what offshore wind energy is: it is a source of clean and renewable energy obtained by harnessing the power of the wind offshore, where it reaches a higher and more constant speed due to the lack of barriers. Its high potential and strategic added value, both at a socioeconomic and environmental level, make it one of the renewable sources that will play a crucial role in the decarbonisation process.
Floating offshore wind, based on floating structures rather than fixed structures, offers new opportunities and alternatives. Basically, it opens the door to sites further offshore by allowing the deployment of wind turbines in larger and deeper offshore areas with higher wind potential. It thus overcomes a stumbling block to providing clean, inexhaustible and non-polluting energy for a more sustainable planet.
Among the advantages of floating offshore wind are the potentially low environmental impact and the ease of manufacture and installation, as the floating turbines and platforms can be built and assembled on land and then towed to the offshore installation site. In addition, as noted above, they can take advantage of the strong winds blowing in the deeper areas, which improves energy efficiency.
Floating offshore wind power in 3D.
The first floating offshore wind farm in Spain (Spanish version).
How does floating offshore wind energy work
To find out how floating offshore wind energy works, we must first answer the following question: Why do wind turbines float in the sea as structures 120 metres high and weighing thousands of tons? The solution was given by Archimedes 2,300 years ago: "a body totally or partially submerged in water experiences a vertical upward thrust equal to the weight of the water dislodged".
A floating offshore wind platform (FOWP) is the concrete, steel or hybrid substructure on which the wind turbine is installed, providing it with buoyancy and stability. Some call it a "floating foundation", but this term is not correct because floating platforms are not founded on the seabed, but are anchored and moored.
Floating wind farms are made up of wind turbines that are placed on floating structures and stabilised by moorings and anchors, and by the way the design of the structure distributes the masses and weights. From there, the process is the usual one: the force of the wind turns the blades and the wind turbine converts the kinetic energy into electricity, which is transported by underwater cables to an offshore substation and from there to an onshore substation on the coast and finally to homes via the power lines.
In addition to floating, wind turbines must produce as much energy as possible, and to do this it is essential that they remain stable, minimising any movement and ensuring that they operate under optimum conditions. This is where the different types of floating platforms for wind turbines come into play, which we will review below.
Types of floating platforms for wind turbines
Floating offshore wind energy is based on floating platforms for wind turbines. The choice of one type or another will depend on sea and seabed conditions, the winds in the area, the size of the wind turbine, the depth of the harbours, the manufacturing facilities or the availability and price of materials and equipment. Some of these are described below:
-
Barge. The concept is similar to that of a ship in terms of dimensions. In other words, the beam and length (length and width) are significantly larger than the draught (height). The floating platform has a large surface area in contact with the water, which is precisely what gives it stability. Like boats, they are made to move to avoid overstressing and stresses on the structure. To minimise these movements, the platform is usually fitted with heave plates, which are surfaces below the waterline.
-
Semi-sumergible. This design seeks to minimise the surface area exposed to the water, but always maximising the volume, which is what really displaces the mass of water and provides buoyancy. Geometrically, the ideal would be a sphere (maximum volume with the smallest surface area), but a sphere is not practical to manufacture, so the volumes that provide buoyancy are divided into several vertical cylinders (or parallelepipeds), which are joined by beams and braces to create a surface where the turbine can be installed. Their size and the distance between them determine their stability.
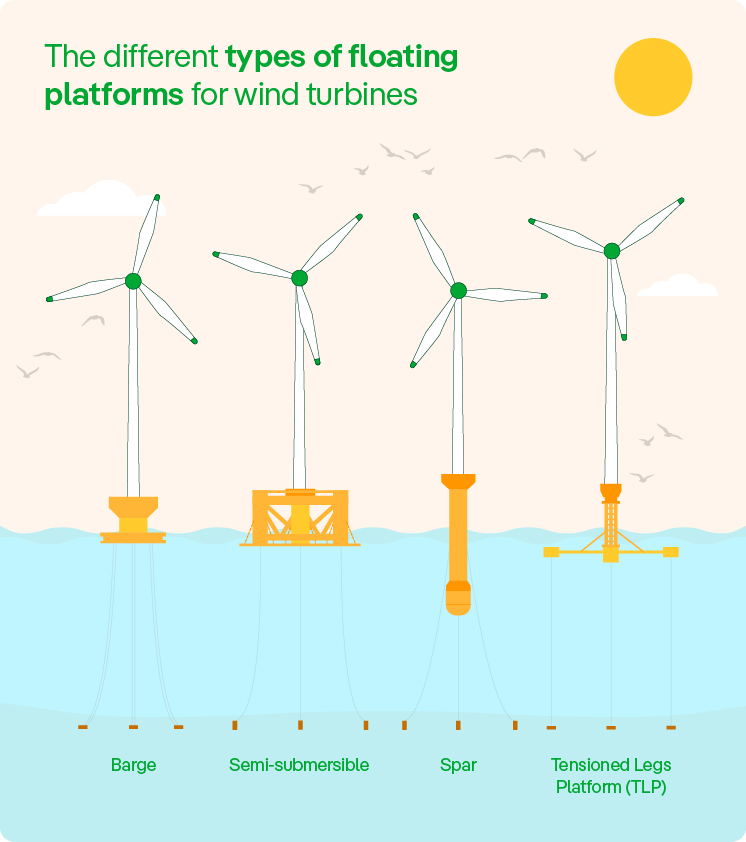
SEE INFOGRAPHIC: The different types of floating platforms for wind turbines [PDF]
-
Spar. In this model, most of the weight is placed at the lowest possible point to provide stability. For example, if we throw a hollow, watertight cylinder into the water, it will float if the ratio of the height to the surface of the base is sufficient for the volume of water displaced to compensate for its weight. If the cylinder is homogeneous, it will not be stable floating vertically and will tip over to float horizontally. To avoid this, the cylinder is provided with a lot of mass at the end opposite to where the turbine is installed to maintain verticality. In short, buoyancy is provided by the geometry of the cylinder, while stability is provided by the weight at the lowest point. As turbines become larger and larger, it requires very long cylinders to compensate for the weights, which makes this solution very difficult to manufacture, transport and install.
-
Tensioned Legs Platform (TLP). The newest and currently most technically risky concept: the platform does not actually float as such once the turbine is installed on it. The aim is to reduce the dimensions as much as possible in order to lower the manufacturing costs. The star geometry of three, four or five arms reduces the volumes of each arm to a minimum so that the platform floats without a load, i.e. without the wind turbine installed. Prior to installation, to prevent the assembly from turning over as the centre of gravity of the assembly rises, temporary, reusable floats are attached to the TLP platform, which in turn allows it to be towed to the offshore anchorage site. Once there, tensioned steel cables or tendons are connected and the temporary floats are disconnected for reuse on the next TLP platform to be installed.
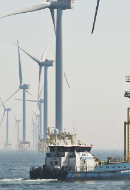
History of offshore wind energy
Discovering the evolution and impact of offshore wind energy.
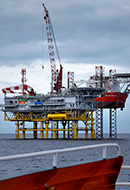
Construction of an offshore wind plant
Everything about offshore wind farm construction.
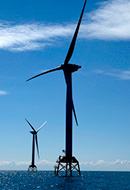
Evolution of wind energy in Europe
The European wind market has grown strongly over the last 25 years. Find out more.
All the information about
Floating offshore wind
Why are floating wind farms made?
The wind speed and frequency is higher and more stable at sea than on land, as there are no obstacles to limit its path (a concept known as fetch). In addition, being located far from the coast minimises the visual impact. Another reason is that most of the fabrication and assembly work can be done in port, with the unit then being towed to the offshore site. This avoids the use of the installation vessels required for fixed foundations, such as jack-up or dynamic positioning vessels (very expensive and scarce vessels that condition the installation times and costs of these foundations). The installation of floating platforms, on the other hand, mainly requires relatively frequent and cheaper tugboats and cable-laying vessels.
At what depth can floating wind turbines be installed?
Generally, it is assumed that floating wind farms will be installed at depths that fixed foundations cannot reach for technical or economic reasons. However, the depth boundary between fixed and floating wind farms is becoming blurred. New configurations are being studied to allow floating platforms to be installed in relatively shallow waters, specifically in locations where seabed conditions pose a risk to the installation of fixed platforms. Currently, it is technically feasible to install floating platforms between 60 and 300 metres, and studies are underway to extend this range to shallower waters, up to 30 metres, or deeper, up to 800 metres, although this is not economically viable at present.
What are the differences between a floating wind platform and a floating oil platform?
Prior to floating platform designs for wind turbines, the oil industry had already used floating platforms for its extraction facilities and many of the concepts have been transferred from one industry to the other. However, the designs are not directly extrapolable. The main differences are:
-
The loads on a floating wind platform are mainly dynamic due to the wind turbine, whereas on a floating oil platform the installed equipment transmits mainly static loads.
-
An offshore oil well concentrates production in a single unit, so the design can be conservative and redundant. In an offshore wind farm, power generation is distributed over dozens of units, so the design must be more efficient to keep costs manageable.
How is energy exported from an offshore wind farm?
Wind farms evacuate the energy produced from their transformer station via a power line to a distribution substation, which carries it to the end user. If the offshore wind farm is located close to the coast, it can evacuate the electricity via an export cable directly to an onshore substation. On the other hand, if they are located far from the coast, an offshore substation (floating or grounded) is needed to raise the voltage of the power generated by the turbines (usually from 66 kV to 220 kV) and allow it to be sent to an onshore substation from where it is distributed.
What are the movements of a floating platform?
The names of the movements are inherited from the naval engineering nomenclature:
-
Linear movements in the horizontal: Surge and sway. The wind turbine is not always in the same position, but depending on the flexibility of the moorings and the depth of the sea, it can move between 20 and 50 metres around a central point.
-
Movement in the vertical: Heave. It is important to minimise this movement through the design of the floating platform, as it affects the position of the hub (centre point of the wind turbine rotor) and the wind speed is directly related to the height.
-
Angular movements: Roll, yaw and pitch. These movements have to be minimised to avoid accelerations at the turbine level, which is more than 120 metres above sea level. A small angular displacement at the level of the floating platform, for example, translates into a large linear movement at the highest point of the structure, which, if not controlled, can damage and reduce the lifetime of the mechanical elements located in the nacelle, which is the three-storey building-sized enclosure housing the electromechanical equipment responsible for transforming wind speed into electrical energy.
What is the mooring?
It is the element that fixes and flexibly connects the floating platform to the anchoring point on the seabed. They usually consist of chains, steel cables or cables made of synthetic materials. The choice of one type of mooring or another depends on the depth, the type of floating platform and the meteorological conditions (waves, currents, winds):
-
In catenary. This is the shape that the mooring or cable adopts when it is not tensioned and the main factor that gives it shape is its own weight, and it is the most frequent. In this case, the moorings are not tensioned beyond the load of their own weight. Depending on water depth, platform movement restrictions and materials, floats and weights can be added to the moorings to modify the shape of the catenary to "S" or similar configurations (lazy-wave).
-
Taut mooring. When a catenary mooring is mechanically tensioned, the aim is to reduce the mooring footprint (affected seabed area), and the length of cable or chain used, and to increase the restrictions on the movement of the floating platform.
-
TLPs (Tensioned Legs Platforms). TLP anchorages are tendons that function differently from tensioned catenaries. They are suitable for large depths due to the material savings involved.
What are anchoring systems and what types are there?
Anchors are the elements that connect the moorings to the seabed. They are used in floating offshore wind turbines and depend on the characteristics of the seabed and the loads:
-
Dragging anchors. Similar to those used by ships. This system supports tension in one direction (with a certain tolerance angle).
-
Suction buckets. Steel structures (usually cylindrical) open at the lower end that rest on the seabed, on which suction is exerted to create a pressure difference (vacuum) and cause anchoring. They need a balanced seabed texture (sandy or sandy-loam) to work properly and are not suitable for rocky or coarse-grained seabeds. Those with a predominantly vertical dimension are usually called suction piles and those with a square geometry are called suction caissons.
-
Driven or drilled piles. These are the same structures used in fixed foundations to anchor the substructure to the seabed. Generally, they are large hollow metal cylinders that are hammered into the seabed (in the case of rocky or hard soils, it is necessary to drill to install them). These piles require special boats for their installation, during which noise and suspended sediments are produced. For this reason, in floating wind projects, their use will be reduced to locations where conditions make the use of other alternatives impossible.
-
Dead or gravity anchors. These are massive concrete structures superimposed on the seabed. They usually have a very large footprint on the seabed, so it is preferred to limit their use to very specific situations and thus minimise their impact.