What is a SCADA system? Discover its advantages
How SCADA works in power grids and power plants
In a scenario where efficiency and security in energy management are key, SCADA systems play an essential role in industrial automation. These tools make it possible to monitor and control critical infrastructures such as electricity grids, wind farms or hydroelectric power plants in real time. They make it possible to optimise performance, anticipate incidents and guarantee a stable and reliable supply of power. Learn more about this technology that functions as the man behind the curtain in energy operations.
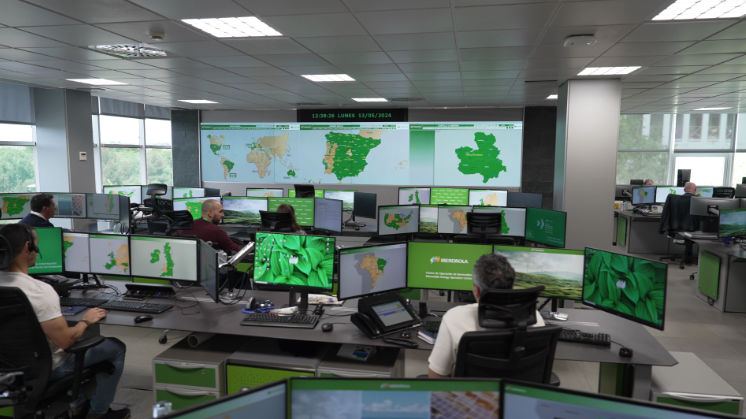
A SCADA (Supervisory Control and Data Acquisition) system is a software and hardware solution that enables real-time monitoring, control and data acquisition in industrial and energy infrastructures. Through sensors, controllers and digital platforms, these systems collect and process key information, facilitating decision-making and optimising the operation of complex installations such as power grids, generation plants and power distribution systems. These tools make it possible to automate processes.
SCADA systems are very useful for improving efficiency and safety in strategic sectors. They can automate management of critical and relevant processes, reducing the margin for human error and optimising the use of resources. In energy, for example, they can balance electricity production and demand, detecting grid failures and preventing incidents before they become major problems. By enabling real-time monitoring, managing companies can respond quickly to anomalies and problems, minimising downtime and improving supply reliability.
SCADA systems are applied in one way or another throughout all industries. In addition to energy, they are particularly important in the electricity industry, chemical and petrochemical plants, water treatment and distribution, logistics and transport systems, and manufacturing and automotive.
Functions of SCADA systems
Thanks to the versatility and variety of applications, SCADA can control and monitor a wide range of industrial processes, from managing energy flows to predictive maintenance of machinery and infrastructures. Some of their basic functions are:
Evolution of SCADA systems
The first SCADA systems emerged in the 1960s as a solution to monitor and control industrial processes more efficiently. In their early days, they were based on analogue technologies with limited processing power, with modest data collection and control systems that relied on local networks and physical servers.
With the advancement of computing and telecommunications, these systems evolved into more sophisticated digital platforms, incorporating communication networks, data visualisation tools, advanced databases and artificial intelligence. Over time, online connectivity gained prominence with significant advances in cyber security to protect the most important or mission-critical systems. Today, SCADA is increasingly integrated with technologies such as the Internet of Things (IoT) and cloud computing, enabling more efficient and secure management of critical infrastructures globally.
Main parts of a SCADA system and how it works
A SCADA system is a technological solution that combines hardware and software to efficiently monitor and control industrial processes. Its operation is based on the interaction of several key components, such as Remote Terminal Units (RTU), Programmable Logic Controllers (PLC) and Human Machine Interfaces (HMI), which work together to collect real-time data, process it and enable remote control of equipment. In an increasingly automated industrial environment, SCADA systems have become essential to ensure the safe, efficient and effective operation of facilities.
How does a SCADA system work? The case of a power grid system
A SCADA (Supervisory Control and Data Acquisition) system monitors and controls in real time the generation, distribution and transmission of energy in electricity grids. This tool enables the electricity system’s efficient, secure and automated management.
-
Level 4 Production scheduling
-
Level 3 Production control
-
Level 2 Plant supervisory
-
Level 1 Direct control
-
Level 0 Field level
SCADA computer centre
SCADA supervisory server for the whole system
SCADA computer SCADA computer
RTU* PLC* RTU* PLC*
Sensors Actuators Sensors Actuators
Plant
SCADA supervisory server for the whole system
SCADA computer SCADA computer
RTU* PLC* RTU* PLC*
Sensors Actuators Sensors Actuators
Plant
*RTU: Remote Terminal Units
*PLC: Programmable Logic Controllers
Source: Techtarget.
SEE INFOGRAPHIC: How does a SCADA system work? [PDF]
SCADA systems are integrated with other control and automation systems through standardised protocols that facilitate communication between devices. This architecture allows data to flow efficiently and in real time, which is crucial for to monitor and control industrial processes. Certain platforms also facilitate smoother integration by combining device programming and configuration in a unified and integrated environment.
The objective is to achieve stable alarm and event management to ensure safety and operational efficiency. SCADA systems are designed to detect abnormal conditions or deficiencies through continuous monitoring of critical variables. When certain preset thresholds are exceeded, automatic alerts are generated to notify operators of the situation. These alerts are classified according to their severity, allowing operators to prioritise responses to critical events. A detailed log can also be maintained, making further analysis and the identification of trends or recurring problems possible.
A reliable communications network is required to ensure secure data transmission between all components of the system. Generally, a hierarchical architecture is used that includes local area networks (LAN) for internal communication and wide area networks (WAN) to connect different facilities or remote sites. Data flows seamlessly from the field devices to the central SCADA server.
But human supervision, of course, is key. Human–Machine Interfaces (HMIs) used in SCADA systems are fundamental to facilitate interaction between operators and the system. There are different types of HMIs, from simple touch screens to more advanced web interfaces that allow remote access even through mobile devices. Progressive innovations in visualisation and technical control significantly improve decision making.
It is particularly important that the entire SCADA system is subject to a cybersecure data environment. The implementation of secure protocols, such as encryption and strong authentication mechanisms, helps to protect transmitted information from unauthorised access. In addition, regular audits are conducted and standards applied to ensure that security practices are aligned with industry best practices, ensuring a secure and reliable operating environment.
Differences from other automation systems in the energy industry
SCADA systems are just one option within the entire industrial automation ecosystem, and while they share certain functions with other technologies, they have key differences in their approach and application.
SCADA and Manufacturing Execution System (MES)
One of the systems that is often compared to SCADA is the Manufacturing Execution System (MES), a technology focused on managing and optimising production within industrial environments. It interconnects all levels of production plants to calculate the efficiency of operations and improve efficiency. It also facilitates the ability to anticipate future issues with a constant information flow from real-time data collection.
Both are systems that can complement each other, improving process performance. SCADA provides operational data and MES uses it to improve planning and strategic decision making. Their current applications are a clear example of this difference: SCADA is common in areas such as power grids, wind farms and substations where it is essential to react immediately to changes or failures, while MES is often used in factories producing electrical components, batteries or turbines, where the aim is to improve productivity and reduce waste.
SCADA and Programmable Logic Controllers (PLCs)
Programmable Logic Controllers (PLCs) are physical devices that execute programmed instructions to control specific processes, such as activating a turbine or regulating the voltage in a substation. SCADA can manage and supervise multiple PLCs within a network to enable constant monitoring and remote control.
A practical example in the power sector is when SCADA is used to monitor an entire electricity distribution grid, while PLCs control individual circuit breakers and transformers within the grid.
SCADA and Distributed Control Systems (DCS)
Distributed Control Systems (DCS) allow processes to be managed by controllers distributed throughout an installation and connected via a communication network. They make it possible to manage a large number of control points, making them useful in large and complex plants.
In power, SCADA and DCS are applied in different ways. While SCADA gives the possibility of managing several connected solar plants in different applications, the DCS system controls the internal processes in a single power plant.
SCADA and Energy Management System (EMS)
Energy Management Systems (EMS) optimise energy consumption, distribution and generation. With them you can analyse patterns and make decisions on how a factory can be more efficient and reduce costs.
In power, EMS takes a more panoramic view. For example, SCADA monitors a power grid and can detect a voltage drop in a substation, sending an order to activate a backup source and prevent a blackout. However, EMS analyses operational data (including data collected by SCADA) and allows redistribution of the electrical load from one generation plant to another to maximise efficiency. Both systems can be integrated at the same time.
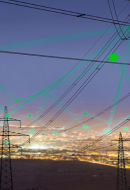
Innovation in networks
Driving smart grids and digitisation.
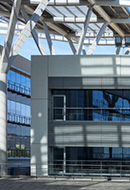
Our innovation hubs
We promote training and research.
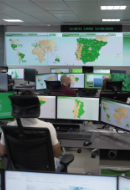
CORE
Iberdrola renewable energy operation centres: 20 years at the forefront of technology.
What are the advantages of SCADA systems over other systems?
SCADA systems stand out from other control systems due to their capacity for real-time supervision, advanced automation and immediate response to anomalies, issues or changes in operating conditions. Unlike systems such as PLCs, which only control individual equipment, SCADA coordinates multiple devices in complex energy infrastructures, allowing centralised and efficient management. Its ability to collect and analyse large volumes of data makes it an essential tool for operational decision making. Some of the key advantages are:
SCADA system in Iberdrola
At Iberdrola España we employ SCADA systems in our operations, including our 4 existing Renewable Energy Operation Centres (CORE) and hydroelectric plants (in Spain we have the COHI). In the UK, Iberdrola's Remote Control Centre (RCC) (Whitelee), through our subsidiary ScottishPower Renewables, operates as a CORE that monitors the operation of onshore and offshore wind farms located in the area in real time. This centre uses a SCADA system that handles more than one million variables per minute, ensuring that the farms remain operational more than 97% of the time. This technology is also applied at the National Control Center (our CORE in Portland, US), the Spanish Renewables Operation Centre (Toledo) and the Brazilian Renewables Operation Centre (Rio de Janeiro).
In addition, we also maintain SCADA systems in several of our mini-hydro plants in Spain, implementing the INGECON HYDRO Manager, a platform developed by Ingeteam based on the Ingesys IT SCADA system, for supervision, control and data acquisition in these hydroelectric plants.