Logistical challenges during the construction of our renewable energy facilities
Discover the main logistical challenges in the renewable energy sector
The construction of renewable energy facilities faces a number of challenges ranging from the transportation of individual components to the management of tenders and contracts for the various major equipment and many others. A good logistics and tracking organisation is essential to overcome potential disruptions in the global supply chain and to reduce the risks, damages, complexities and costs inherent in the projects.
December 2022
Approximately 9 minutes
Building and commissioning renewable energy infrastructures is a challenge in which countless unforeseen events and obstacles can arise. One of the main tools for tackling this ambitious task is good logistics that allows the definition of the precise deadlines, means and processes to efficiently fulfil the service.
But foresighted organisation not only includes the transport of parts, but also all the activities necessary to ensure that supplies reach the installation site, that imports and exports comply with international regulations or that possible storage needs for materials can be defined, among many others.
Step-by-step logistics in renewable energy plant construction
Each of the steps prior to the construction of a renewable energy installation is important and must be carried out with attention to detail to avoid any failures or unforeseen events. The phases of this logistics management are:
Offer and recruitment
Before acting, planning is necessary. Every logistical process must start with a definition of the strategy to be followed, which answers different questions: Where will the manufacturing take place? Does the process involve any import or export? What transport options are available? What are the dates of need for the installation? In addition, the logistical (e.g., packaging, storage and preservation) and, of course, monitoring requirements must be established.
Launch of the supply
Subsequently, the scope and requirements of the supplies needed should be reviewed. At this point it is necessary to consider who should be informed of progress and to plan activities for monitoring at source.
Manufacture
The collection of materials and subcomponents is carried out, the manufacture of the different equipment and components is started, and monitoring and communication is maintained with suppliers, the rest of the areas involved and those responsible for each project.
Exports and imports
This phase involves a careful review of the sales contracts to conform to the rules of International Trade. The most appropriate Incoterms, responsibilities and documentary and financial processes of the transactions are defined.
Transport
Prior to construction, the operation is fine-tuned and follows the transport strategy defined by the contract and the needs of each project. Execution also involves precise supervision to ensure that all equipment and components are delivered at the right time.
An overview of the main logistics challenges
The challenges that beset the construction of a renewable installation are as varied as the number of actors involved and tasks involved. Here are some of the main challenges:
Stockpiling and storage of materials
Planning for potential material stockpiling and storage needs can reduce the number of unforeseen events during the construction of the renewable installation. This is the case for photovoltaic projects, which have a streamlined and systematised installation process and require a careful strategy to avoid material shortages that interrupt construction.
Photovoltaic modules are typically manufactured in Asia and, in a context of high demand, it is particularly important to manage early procurement processes. It is also essential to ensure the availability of storage space for materials in a location close to the parks to allow for quick and serial supplies.
Global supply chains
The logistics of renewable projects, as part of the global supply chain, suffer from product shortages, stock-outs, transport difficulties, and price and lead-time increases. In addition, in many cases, manufacturers renegotiate their contracts upwards to try to compensate for losses.
Renewable projects therefore face challenges due to the interdependence and fragility of the global supply chain, which can lead to delays and production stoppages.
Transport of major equipment
Transporting the main supplies and equipment is one of the most important parts of the construction of a renewable installation. And this translates into significant economic weight: in onshore wind farms, for example, transport accounts for approximately 7-10 % of the project cost, sometimes even more depending on its manufacturing origin and operational difficulty.
If we focus on this type of wind farms, transport is a real challenge for logistics. Both the dimensions and the weight of the wind turbines are increasingly larger to improve their efficiency, which makes their mobility more complicated, to the point of becoming a limiting factor in their design. In addition, these projects are usually located in high mountain areas with steep access slopes and very sharp curves.
In general, the logistics at this point involve a detailed route study and transport strategy. The shovels are the longest element: each shovel can reach more than 80 metres and weigh several tens of tonnes. In this type of transport, specialised vehicles are needed that allow great mobility in order to successfully manage the curves of the routes, especially on county roads and access roads to wind farms.
In extreme cases, a very special transport configuration called Blade Lifter is used. This technology lifts the shovel by means of a mechanism, usually a hydraulic lift, to reduce turning radius and shovel interference when turning, making it easier to drive on narrow roads or even in urban areas.
The system makes it possible to transport blades up to 80 metres long on roads with sharp bends.
The rear trailer is coupled to the assembly for improved manoeuvrability.
The blade is tilted up to 60º above the horizontal axis, shortening the assembly.
The blades can be rotated 360° while driving (e.g. to avoid the wind). A third vertical rotation axis allows a lateral angle of 20°. A very useful option in heavily built-up areas.
An operator accompanies the Blade Lifter on foot, with a remote control to adjust the position of the blade.
Maximum wind speed for transporting the lifted blade.
BLADE LIFTER
This system of tilting the blades during transport reduces the environmental impact, avoiding changes in road layout.
This system of tilting the blades during transport reduces the environmental impact, avoiding changes in road layout.
The blade is tilted up to 60º above the horizontal axis, shortening the assembly.
The system makes it possible to transport blades up to 80 metres long on roads with sharp bends.
The blades can be rotated 360° while driving (e.g. to avoid the wind). A third vertical rotation axis allows a lateral angle of 20°. A very useful option in heavily built-up areas.
The rear trailer is coupled to the assembly for improved manoeuvrability.
Maximum wind speed for transporting the lifted blade.
SEE INFOGRAPHIC: Blade Lifter [PDF]
As with the blades, the nacelles —the part of the wind turbine that houses the main mechanical and electrical elements— are notable for their large size and weight. Their width and height measures around 4 metres or even more, while their weight has made it necessary in recent years to design them in such a way that they can be transported in several separate pieces in order to make them easier to transport and install. The same is true for towers -which have to be transported in several sections (4 to 7 depending on the hub height) and weigh between 50 and 80 tonnes.
In the case of offshore wind, manufacturers have tended to locate their facilities in areas with easy access to the sea or rivers to facilitate sea or river transport. From there, the components begin a journey by ship to the marshalling harbour where they are assembled and then transferred by installation vessel to the assembly point at sea.
In the case of Green Hydrogen projects, the most complicated logistics are centred on the hydrogen storage tanks or columns. These tanks are very thick, which results in weights of around 80 tonnes per unit, and their oversized width and length mean that they have to be treated as special transports.
The components of hydropower plants —turbines, generators, transformers, large penstocks, etc.— are also very large. In addition, the routes and characteristics of the roads along which they must travel, with steep slopes, pose a challenge for logistics, which must seek solutions for efficient mobilisation.
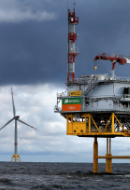
Innovation in renewables
We innovate to improve the efficiency of our renewable assets.
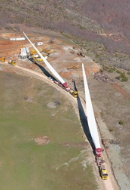
Blade Lifter
The new transport system for wind turbine blades.

Where to install a wind turbine?
Discover the system that calculates the most suitable locations.
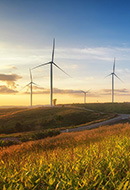
Wind measurement
How a wind measurement study is carried out.
Carbon footprint of transport
Reducing greenhouse gas emissions from transport is another major challenge. The aim is to make renewable projects as sustainable as possible at every stage of their construction.
Some solutions involve selecting production plants closer to the wind farm locations or grouping sea shipments of different components and projects in order to reduce the number of freight charges required.
New propulsion technologies are currently being developed for ship engines that are powered by ammonia instead of heavy fossil fuels. But if this ammonia is also produced from green hydrogen, as Iberdrola is already doing, and, in turn, the expansion of transport using electric motors is achieved, the carbon footprint associated with the logistics of renewable projects will be substantially reduced.
How does Iberdrola address these challenges?
Iberdrola relies heavily on different actors to meet these logistical challenges: major technologists who manufacture the main equipment, transport suppliers, storage platforms, port facilities, assembly and installation companies, etc.
However, Iberdrola has a Global Logistics Services area that has extensive experience in the worldwide transport of all types of large equipment for various projects and in the supervision and performance of all types of logistics operations in order to reduce the risk of supply processes in projects, while seeking maximum efficiency in terms of time and cost.